What Happens to Your Inventory Inside an Amazon Warehouse?
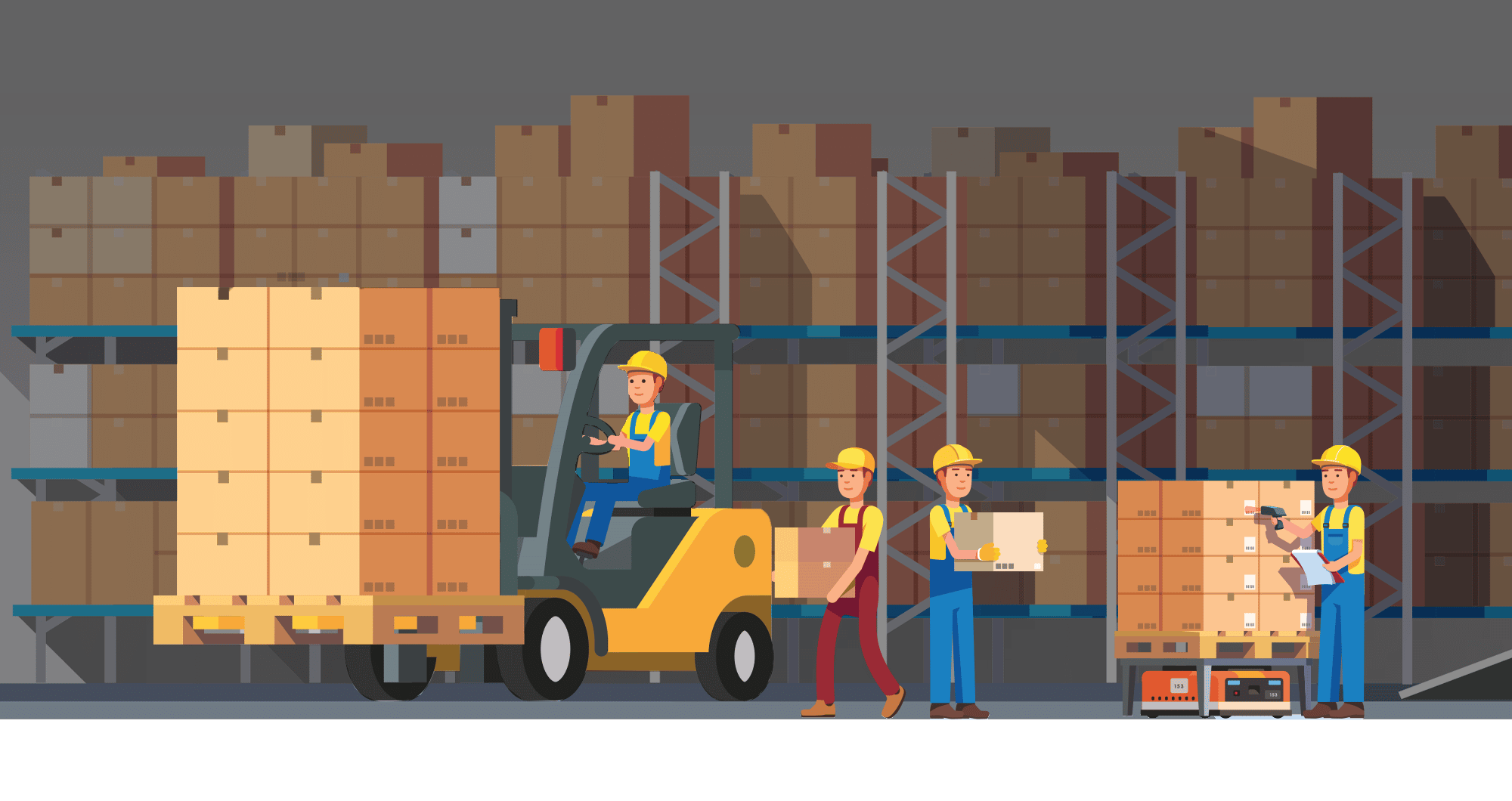
After haggling endlessly with your supplier from China, you finally have your products ready to ship to one of Amazon’s hundreds of warehouses. As an ecommerce company, it’s completely normal to have no visibility on your products before they reach your customer’s doorstep.
In this article, we’ll take a look at what your inventory goes through in an Amazon warehouse before they are delivered to your buyers. We can finally learn and have some visibility into our products before they’re shipped out.
Spoiler alert: It involves overpriced robots and overworked associates.
Contents
The Critical Feature: Amazon FBA
Customers can't shop directly from an Amazon warehouse, but there are hundreds of Amazon fulfillment centers that make delivery faster. As more third-party sellers came into the picture, Uncle Jeff thought it was a good idea to make things easier for them in terms of fulfilling orders.
When Amazon first started seeing more third-party sellers come into the picture, Uncle Jeff thought it was a good idea to make things easier for them in terms of fulfilling orders.
Thus, in September of 2006, FBA was launched, and it was a godsend for ecommerce entrepreneurs. With FBA in place, it makes it easier for third-party sellers to ship out orders to their customers. Of course, there are FBA fees involved, but they are generally worth the convenience.
A Look at the Numbers of FBA
Jeff Bezos is one of the richest men in the world, so it will come as no surprise that his company’s real estate is astounding.
As of 2023, there are more than 175 fulfillment centers, the majority of which are located in North America and Europe. These warehouses have a total square footage of approximately 150 million — and these are just the fulfillment centers. There are different types of Amazon warehouses distributed in various locations dedicated to other purposes like sorting and receiving, and there are also specialty centers.
The number even increased during the pandemic when Amazon was doubling down on building more warehouses to meet the demand. Post-pandemic, a lot of these warehouses were closed until the launch of the Amazon Warehousing and Distribution (AWD) which provides a cheaper long-term storage solution to third-party sellers.
If you’re ever in the United States or Canada, you can sign up for an actual tour inside an Amazon fulfillment center in 23 locations. There are also public tours available in Europe.
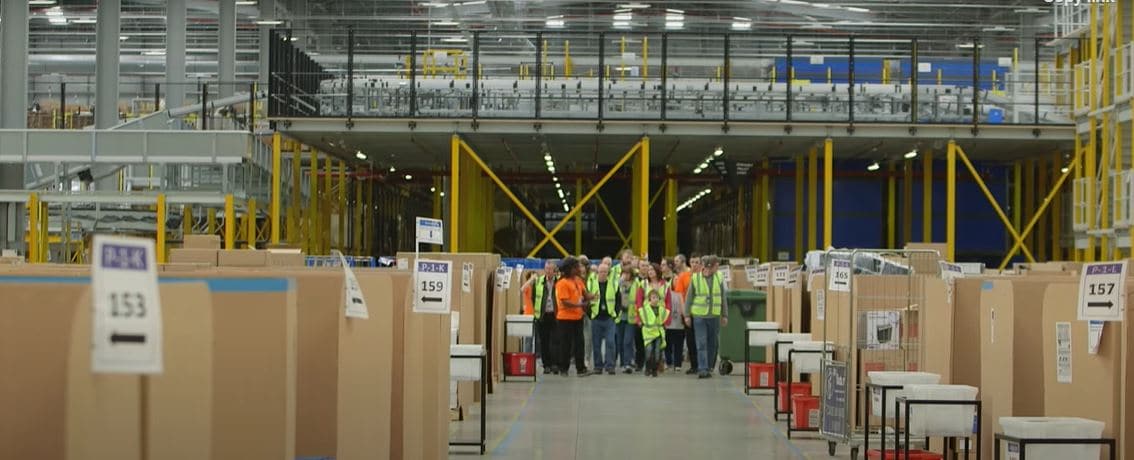
As of July 2020, Amazon has around 1 million employees, but the number will only get bigger during holidays and other peak seasons because of additional demand.
Dave has actually worked for Amazon for a week, and it’s interesting to see a successful third-party seller experience what it’s like to be an Amazon associate.
In terms of revenue, the ecommerce giant raked in USD280.5 billion in 2019, which made its founder so rich that his money is greater than the number of brain cells in an average human.
From Your Supplier to an Amazon Warehouse: 3PL vs Direct Shipping
Let’s say you’re importing from China. Your supplier has already shipped your products and the ship carrying it has arrived in one of the ports in the United States. What happens then?
You can opt to hire a third-party logistics company to handle your inventory or you can ship directly to Amazon.
Some sellers even go the extra mile of having their products sent to their own warehouses (or sometimes houses) to personally inspect them. It goes without saying that this technique will incur additional, and sometimes unnecessary, costs. But some sellers do this to make sure that their products are in pristine condition.
You might want to try this out especially if you’re still new to the industry. New sellers often start out with a few units before finally shipping full containers to Amazon.
There are pros and cons whether you employ 3PLs or ship the products directly to Amazon. In choosing between the two, you have to consider the following:
- The costs involved
- Risk of not being able to inspect your inventory first
- Transit time
If you ship directly to Amazon, you won’t be able to catch problems before the inventory arrives in the fulfillment center. However, it will reduce transit time and touch points, making the chance of damaging the items lower.
How Your Products Are Approved for Storage
When your package arrives in the fulfillment center, it undergoes a rigorous process before it is approved for storage. Well, at least that’s what they expect us to believe.
In reality, however, Amazon associates are instructed to put everything on the shelf that doesn’t have a hole in the packaging that’s greater than the size of a golf ball.
However, it’s still best to be careful with packaging. To avoid delays, you need to make sure that your products are compliant with Amazon’s standards, especially in terms of packaging and labeling.
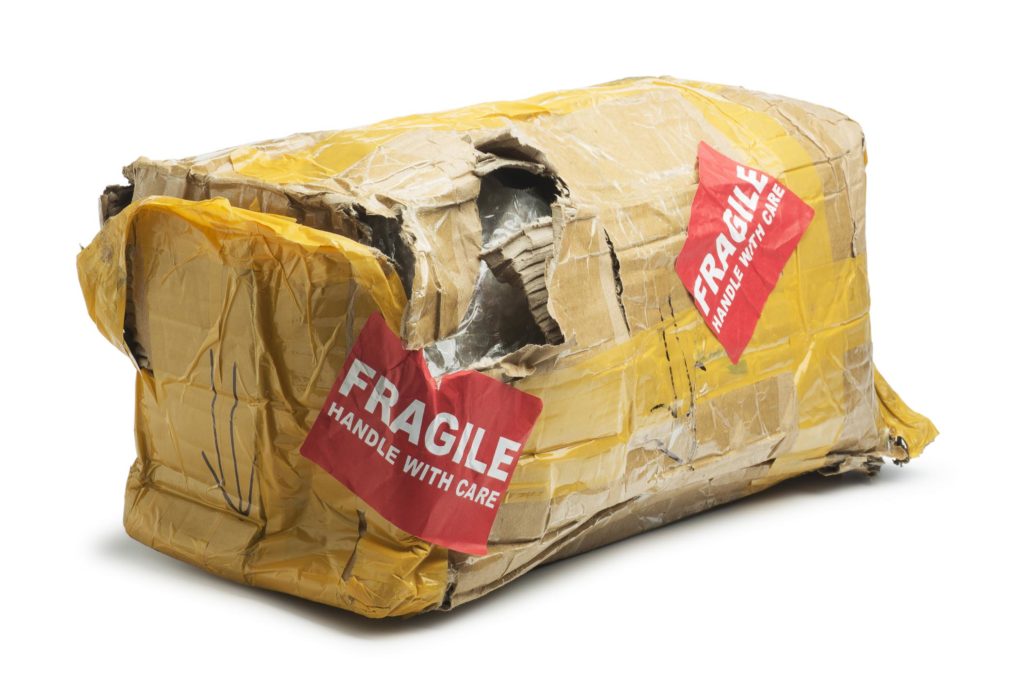
Another important thing to make sure of is that what you're trying to store is not one of Amazon’s restricted products.
Package Inspection and Scanning
You have to make sure that each item is packaged properly and there are different rules regarding packaging. For example, if you’re using a perforated box, it should pass a three-foot drop test. If it fails the test, it should be placed in a polybag with a suffocation warning label.
At the fulfillment center, an Amazon associate inspects your package to make sure that it arrived in good condition, after which, he or she scans the shipping label to make sure that it’s in the correct center.
Speaking of labels, Amazon has specific requirements for labelling products that arrive in its fulfillment centers. For example, products that expire must have the expiration date printed both on the master carton (and must be in 36-point font or larger) and on the individual units. Suffocation warnings are also required for polybags whose openings are 5 inches or more in length when measured flat.

To reduce delay, make sure to stick labels and barcodes on flat surfaces that will not be damaged when the box is opened.
Product Inspection
After scanning the label in the main package, an associate opens the box to inspect the individual items. At this stage, the associate determines whether
- Each unit has one scannable barcode (having multiple will result to dely) and
- Whether there is a need for additional packaging to avoid damages during delivery
Once approved, the items are then delivered to the receiving station where another associate performs a six-sided check, making sure that no items are damaged. If everything looks good, the same associate performs a title verification, after which the inventory is considered officially received.
Product Storing
How and where your inventory is stored inside an Amazon fulfillment center depends on its type.
For example, to avoid shelf wear, media products are stored in library-type shelves in vertical spine out positions with loose stacking. High-value goods may be stored in a more secure area.
What Happens if Amazon Loses Your Products
When Amazon loses your products, the first thing it will do is to try and find them. How long will this take? I hate to be the bearer of bad news, but there’s no definite answer here. For some, it takes a few weeks. For others, the seller could be waiting for months.
If Amazon decides to give up on the investigation, they will reimburse you for the lost goods minus the Amazon fees.
But here’s the catch. If after reimbursement, they eventually locate the missing items, Amazon will get back what they paid you, usually charging it to your next deposit.
How Amazon Makes Sure Your Products Are Not Stolen
You might be wondering at this point how Amazon prevents theft inside the warehouse. With millions of products on the shelves and hundreds of associates on the ground, people may be too busy to notice if an item or two is stealthily removed from the pods.
This is where the security features come in. Every Amazon associate that enters the warehouse goes through a security check akin to those in airports. Phones are strictly prohibited, and each employee is thoroughly checked for any stolen items they might smuggle out of the warehouse.
There are still times, however, when workers try to steal from Amazon. Some of them got caught, and in an attempt to deter the behavior, the company had resulted in Orwellian tactics that added to issues of employee dissatisfaction with the working conditions.
How Your Product Reaches Your Customer’s Doorstep
After being received and stored in the Amazon warehouse, the listing goes live or the number of items are updated. Hopefully, someone will click on your listing and buy your products.
But what exactly happens when a customer clicks on the Buy button?
Here’s when those orange robots come in. If you examine the floors of an Amazon fulfillment center closely, you will see a lot of QR codes. This is how robots move around the warehouse and deliver the appropriate pods to the associates.In 2012, Amazon bought the robotics company Kiva and renamed it to Amazon Robotics. This is the company responsible for making the machines that make fulfillment faster and more efficient.
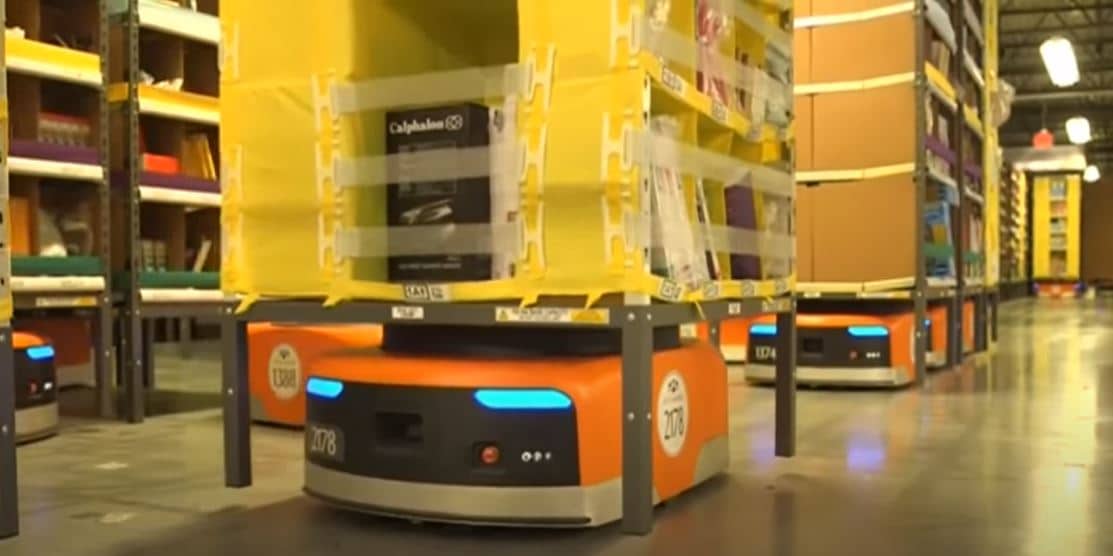
Through these Kiva robots, Amazon associates don’t need to run across the warehouse, which can be as large as a few football fields. These small robots are usually found in warehouses that store standard-sized items. For warehouses that store oversized packages which contain things such as bathtubs and kayaks, bigger robots do the picking and transferring.
The advanced technology allows machines to determine the appropriate pods and deliver them to an associate known as the picker.
Think of a picker like a personal shopper who picks out the specific items you ordered from the pods the Kiva robots deliver. The items are then placed in a tote, those yellow-colored boxes that are ubiquitous in Amazon warehouses.
The items are then delivered to the pack station. Here, Amazon does a great job in ensuring efficiency because they take away all the guesswork since computers know exactly the ideal box the goods should be shipped in as well as the exact amount of tape needed to seal the boxes.
Throughout all these processes, miles’ worth of conveyor belts are utilized to get the products from one place to another. The labels are also pasted on the boxes within seconds. And because employees’ movements and productivity are constantly monitored, Amazon deliveries are getting faster.
After the packages are ready, they are then delivered to the customers. This can be done in various ways.
Amazon partners with third-party logistics including the USPS, but it’s slowly building its own battalion of delivery vehicles to further lessen the costs.
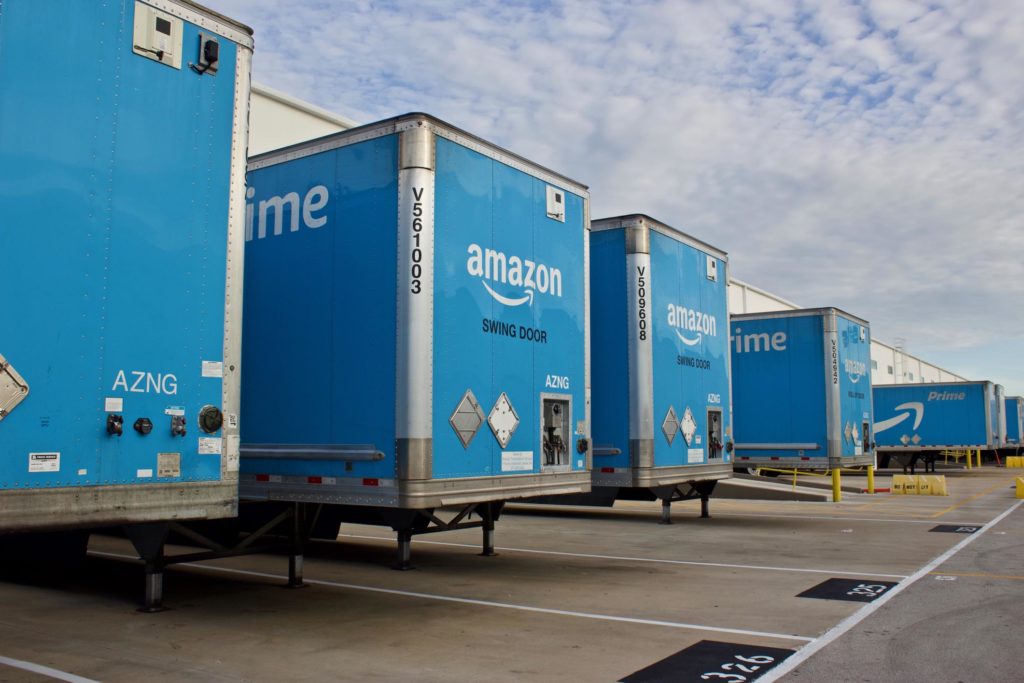
In 2015, for example, Amazon Flex was launched. This allowed individuals who have a driver’s license and are over 21 years old to make some deliveries. Amazon also has about 80 aircraft and is procuring more.
You can also apply to be an Amazon Delivery Service Partner. For as low as $10,000, you can partner with Amazon to help out with logistics. You’ll be like UPS that partners with the ecommerce giant.
You might have even heard of drones being tested for deliveries. It seems like Uncle Jeff and his team will stop at nothing to get your orders shipped to your doorstep as soon as you click Buy.
Conclusion
Amazon has been creating a system that allows third-party sellers to store, fulfill, and deliver their products to customers in the most efficient way possible. It’s safe to say that Amazon FBA has revolutionized the way ecommerce businesses operate.
Your inventory goes through so much inside an Amazon warehouse. Before it reaches your customer, it has to go through rigorous inspections, long conveyor belts, and multiple gloved hands.
It’s no secret that Amazon is leading the ecommerce industry. Its technology is unparalleled and we have yet to see more of what it has to offer.
Have you been on a tour in one of the fulfillment centers? We’d love to hear what it was like for you.
Dear Christine,
Thanks for your great article of the introduction in detail. Recently I met a problem related to this. May I have your kindly opinion?
The question is,I sent some cattons of products to the warehouse of Amazon(FBA) by mistake: the listing is A ,the FBA box labels are A, but the products are B,the labels on the product are also B,so there are the mistakes.
Now it seems the cargo is under checking in, I have already cancelled the shipment but I am afraid the wrong items may be received in stock and delivered to customers by mistake. I opened cases about this on Amazon but did not get clear answers.
Please kindly advise what can I do? Thanks.
Normally Amazon will rectify it and check in product B. If they check it in as Product A it means theyve relabeled your items and you’ll want to recall the inventory though. Happens all the time, for better or worse.